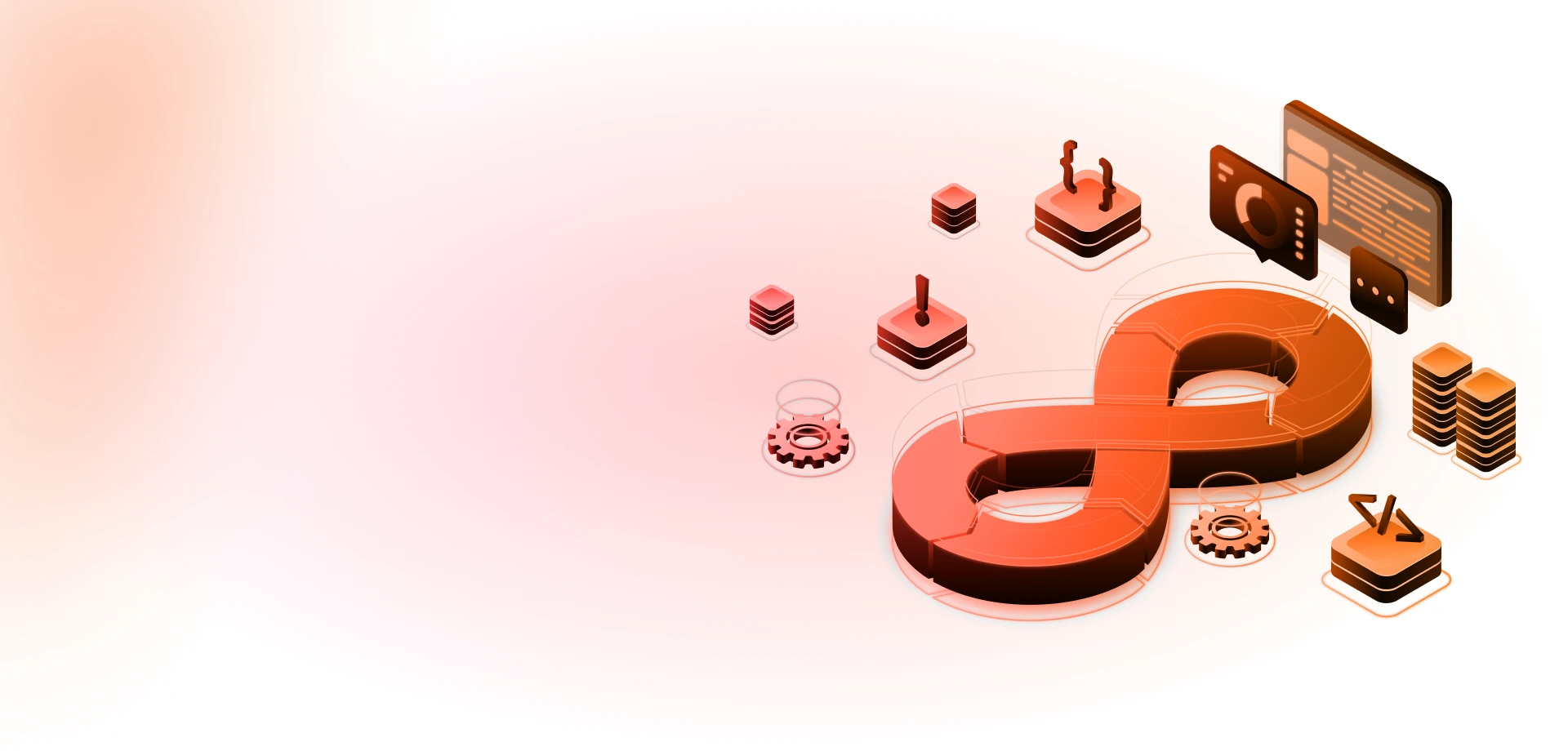
Digital Twin Development Company
With our digital twin services, companies can manage tangible assets such as industrial equipment and advanced infrastructure in real-time, enabling them to emulate and improve them.
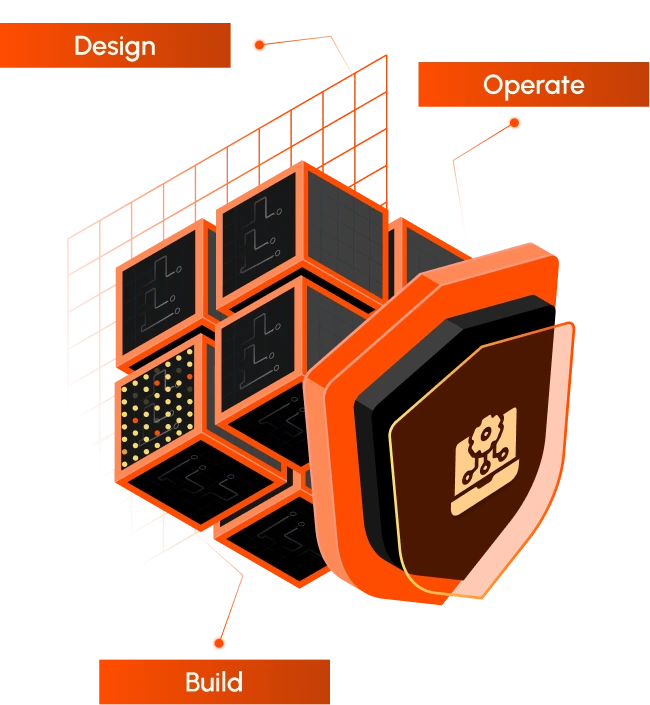
Digital Twin Development
The construction of a virtual, active model of an actual object or system that can perform various functions like simulation, forecasting, and improvement is known as the digital twin.
A new type of technology called Digital Twin Technology is provided by Osiz Technologies, which produces digital representations of physical assets, systems, or processes in real time. Our digital twins are a combination of IoT, AI, and data analytics that enable continuous monitoring, simulation, as well as predictive insights to enhance performance, minimize downtime,and make more informed decisions with data. In sectors such as manufacturing, smart cities, healthcare, and energy, Osiz delivers tailored digital twin solutions that enhance operational efficiency and innovation.
Our Digital Twin Development Services
Custom Digital Twin Modeling
Our goal is to create precise digital depictions of machines, systems, and environments that enable real-time interaction.
Real-Time IoT Integration
Quickly establish physical connections with IoT sensors and enable real-time data transfer to digital models.
AI & ML-Driven Insights
We apply advanced AI and machine learning techniques to deliver powerful predictive analytics tailored to your needs.
3D Visualization & Simulation
Construct engaging, easy-to-understand 3D models and dashboards to observe and replicate real-life situations.
Scalable Cloud Architecture
Create reliable cloud-based systems that grow with your business and can integrate with existing systems.
End-to-End Development
Our digital twin development services are a complete package that covers strategy, design, deployment, and maintenance.
Industries We Serve
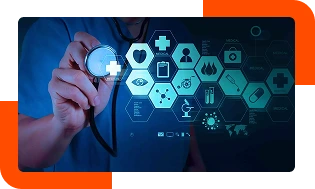
Healthcare
Create personalized digital models for patients to optimize care, quickly track their health, and improve treatment approaches.
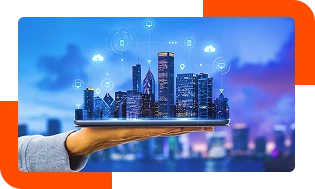
Smart Cities
Enable intelligent infrastructure management, optimize traffic flow, and monitor utilities for better urban planning and sustainability.
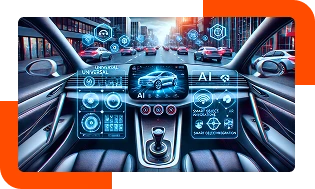
Automotive & Aerospace
Modify design features, supervise safety measures and track asset longevity for better maintenance and efficiency in automobiles and aircraft.
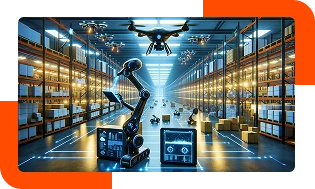
Retail & Logistics
Improve supply chain transparency, reduce warehouse costs, and enhance customer experience through the use of real-time analytics and simulations.
Digital Twin Development Process
Discovery & Requirement Analysis
Our team works together to understand your business objectives, challenges and the systems or assets required for digitalization.
Data Collection & IoT Integration
We gather real-time data from sensors and IoT devices, ensuring that data is seamlessly integrated into the digital model.
Custom Model Design & Development
The digital models we produce are crafted by our experts using precise 3D representations that reflect real-life processes or assets.
AI & Machine Learning Integration
Artificial intelligence and machine learning are utilized by us to provide predictive insights, identify flaws, and automate decision-making processes.
Deployment, Monitoring & Support
Our approach involves implementing the solution, guaranteeing efficient integration with current systems and providing ongoing support for improvement.
Technologies We Use for Digital Twin Development
The tools and platforms we possess are advanced enough to create smooth and precise digital representations of real-world systems.
Internet of Things (IoT)
Cloud Computing
Artificial Intelligence& Machine Learning
3D Visualization Tools
Big Data & Analytics
Edge Computing
Blockchain
AR/VR Technologies
Why Choose Osiz for Digital Twin Development?
Osiz is a leading AI development company offering custom Digital Twin development services and solutions. Our digital twin services include consulting, real-time data analysis, 3D modeling, simulation, and predictive modeling. We also provide end-to-end project management and continuous support to ensure the success of your digital twin initiatives. Our services cover a wide range of topics from initial consultation and strategy development to design, implementation, and ongoing improvement. We use the latest technologies in IoT, AI, machine learning and cloud computing to ensure your digital twin solutions are flexible, secure and well-integrated with your existing systems.
Take the first step in transforming your company's digital footprint by partnering with Osiz Technologies and implementing innovative solutions. Throughout the process, our experts will provide you with ongoing guidance, from the outset to the final version.
"Transform your business with Osiz Technologies" Digital Twin solutions—where innovation meets precision.